ESG Strategy in Action: Connecting Building Operations to Carbon Reduction Goals
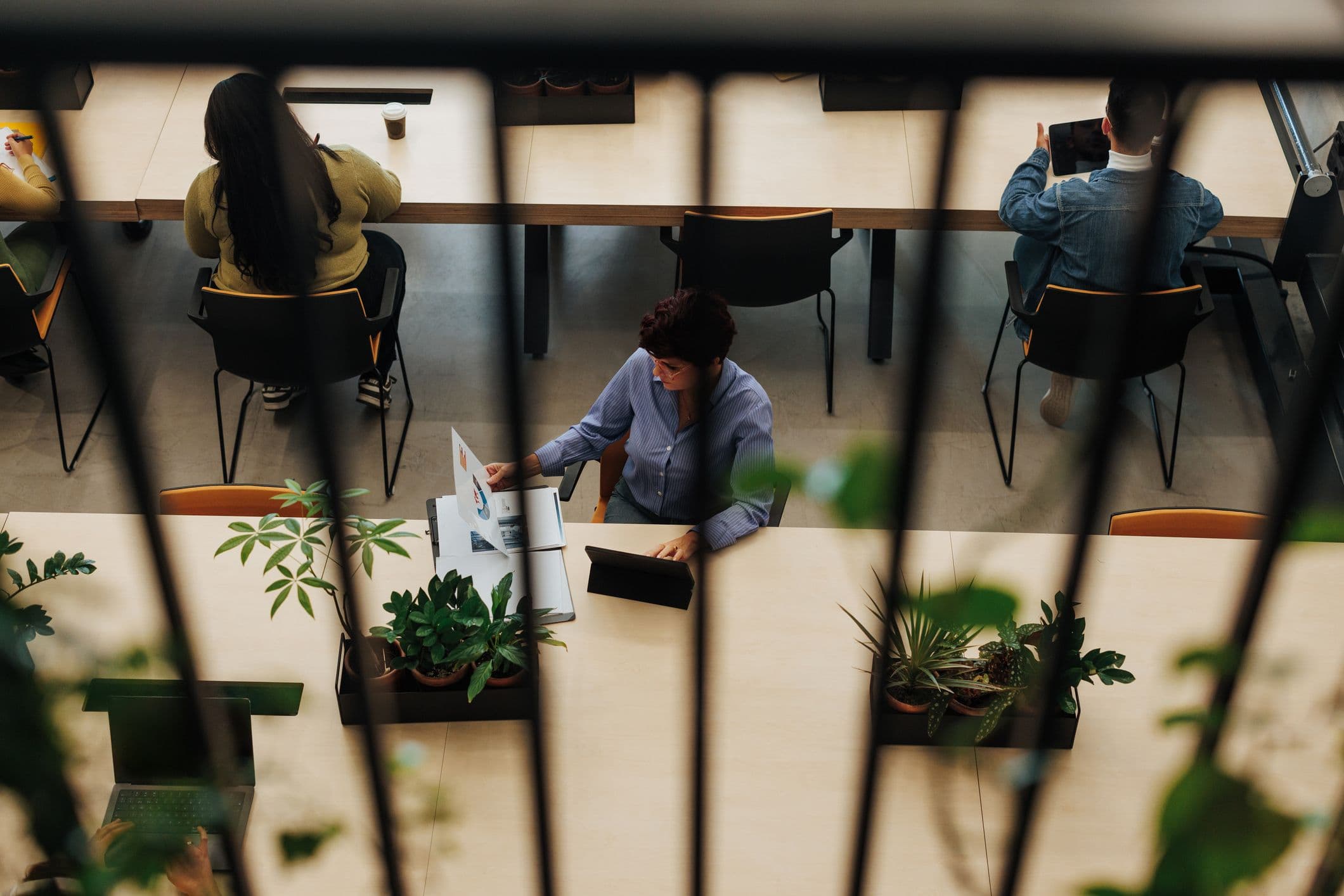
It usually starts with a spreadsheet.
A carbon reduction target is set, a roadmap is drafted, and a reporting framework is chosen. But somewhere in the often-yawning gap between the boardroom and the boiler room, that well-considered plan hits resistance: outdated control systems, inconsistent data, short-staffed facilities teams, or unchecked energy waste hiding in plain sight.
This disconnect between ESG strategy and building operations can stall progress — not due to lack of intent, but rather a lack of integration between vision and reality.
For sustainability goals to move beyond aspiration, they must be translated into operational action — the kind that lives in runtime schedules, setpoints, and chillers. This article unpacks how to bridge that divide with practical strategies, quantifiable outcomes, and the infrastructure (human and digital) to make “ESG” real, impactful, and measurable at scale.
Why ESG Strategies Struggle at the Building Level
ESG targets — whether voluntary or regulatory — tend to be portfolio-wide and abstract: “50% emissions reduction by 2030” or “Net Zero across Scope 1 and 2 by 2040.”
But building systems are hyper-specific. HVAC setpoints, fan runtime, occupancy schedules, maintenance backlogs; these granular, technical details are also among the main drivers of energy use, emissions, and (ultimately) portfolio or corporate ESG performance.
The challenge is thus translating high-level strategy into ground-level action within these complex and fragmented operational realities. Key obstacles include:
- Siloed building data
- Inconsistent metering and monitoring infrastructure
- Distributed operating teams and partners
- Short-staffed engineering and FM teams
- Limited transparency into which systems are driving inefficiencies
Without addressing these friction points, sustainability and ESG initiatives often stall at the reporting layer — producing charts, but not change.
Strategy #1: Connect ESG Goals to Operational Metrics
The first step toward operationalizing ESG is grounding targets in building-level KPIs. This means translating “reduce Scope 2 emissions” into metrics like:
- Energy use intensity (EUI) by building
- Peak demand (kW) and load profiles
- System-level efficiency (e.g., chiller kW/ton)
- Runtime schedules vs. occupancy
Facilities and sustainability teams need shared dashboards, terminology, and data views to collaborate effectively.
Best practice: Create a “translation layer” between ESG targets and operational levers. For example, map out which systems (lighting, chilled water plant, AHUs) contribute most to Scope 1 and 2 emissions, and tie optimization projects directly to those sources.
Strategy #2: Build a Unified Data Infrastructure
Most portfolios rely on a patchwork of building automation systems, smart meters, utility bills, third-party sensors, and even disparate software tools or energy management platforms. The result? Data silos and inconsistencies that make it hard to see where energy is being wasted.
A growing number of organizations are solving this with an Independent Data Layer (IDL) — a vendor-agnostic architecture that ingests, normalizes, and maps data from across systems. Whether built in-house or delivered via platforms like Noda Energy, an IDL forms the foundation for downstream energy analytics, insights, and automation.
Best practice: Use a common ontology (e.g. Project Haystack or Brick Schema) to standardize point names and data types – or work with a partner (like Noda) . This reduces friction during integration and enables consistent, continuous analytics across diverse systems and vendors – and is fit to scale as you onboard new buildings or add/change equipment.
Interested in learning how AI can support you in overcoming building and equipment data challenges? Stream our latest webinar here.
Strategy #3: Go Beyond Monitoring to Fault Detection
Many buildings have energy dashboards, BMS, or basic utility tracking software — but few are effectively using their data to uncover root causes of inefficiency.
That’s where fault detection and diagnostics (FDD) comes in. FDD systems use rules-based logic or machine learning to identify problems like:
- Simultaneous heating and cooling
- Equipment running outside of scheduled hours
- High duct static pressure or flow rate issues
- Occupied zones with inadequate cooling
These insights surface hidden issues and help prioritize action, especially for resource-constrained engineering teams. They can also add significant scale to your efficiency program by eliminating the need for time-consuming, manual checks and audits.
Best practice: Classify faults by ESG relevance. For example, focus first on energy-related faults with large carbon impact, or faults that affect occupant comfort and IAQ (which can tie to the “S” in ESG).
Strategy #4: Identify Energy Optimization Projects That Facility Teams Can Act On
Fault detection and analytics are critical for surfacing operational issues, but one of the biggest barriers to impact is turning those insights into actionable energy projects. Often, busy facility and engineering teams lack the time, context, or coordination tools to move from problem to resolution, and to quantify the resulting impact after the fact.
This is where energy project identification tools come in. Key capabilities often include:
- Grouping recurring or large faults into low-or-no-CapEx optimization projects
- Estimating energy, cost, and carbon savings potential to drive better prioritization for teams on the ground
- Automatically tagging responsible systems or locations
- Assigning tasks across internal teams or external service providers
- Tracking implementation and verification of results
The most successful teams integrate this workflow into their daily operations — not just as a one-time audit, but as a continuous improvement cycle.
What if you don’t have a dedicated platform?
Even without a formal project management tool, organizations can still operationalize this process using a structured playbook and shared documentation systems. Start by creating a standardized template to log recurring issues, their root causes, proposed actions, and estimated impact. Use a shared spreadsheet, internal wiki, or a lightweight ticketing system (like Trello, Airtable, or even Google Sheets) to assign tasks, track progress, and document results. Pair this with regular cross-functional reviews — for example, monthly check-ins between energy managers, facilities teams, and sustainability leads — to prioritize the most impactful projects and share learnings across sites. The key is consistency: simple tools can still drive real change when paired with process discipline and clear ownership.
How to quantify energy and carbon savings without a platform:
To validate the impact of energy projects, it’s essential to translate kWh or therm reductions into financial and environmental terms. A simple way to do this is by maintaining a central reference table with utility-specific blended energy rates (e.g. $/kWh, $/MMBtu) and location-based GHG emission factors (e.g. kg CO₂e/kWh). These can typically be sourced from utility bills, EPA eGRID data, or international equivalents. When projects are completed — such as reducing AHU runtime or optimizing chiller sequencing — teams can calculate savings by multiplying avoided energy use by these rates. Recording these results in a shared tracker (including date, building, system type, and estimated impact) helps build a cumulative view of progress over time — and can directly support ESG reporting, budget forecasting, and capital planning.
Best practice: Use a structured playbook like the above, or a technology platform (like Noda), to find and manage energy-saving initiatives. Make sure projects are accessible to site-level facility operators and sustainability teams alike, and that tracking systems include expected outcomes (e.g., kWh or CO₂e savings) to support ESG reporting and ROI measurement. Whether a big project or small FDD insight, tie every operational action to an ESG metric –e.g. If a chiller optimization project is expected to save 50 MWh/year, quantify the associated emissions reduction (e.g., 25 tons of CO₂e) and update your ESG progress accordingly.
Strategy #5: Leverage Automation When Ready
If you’ve mastered FDD and energy project management, the next frontier is automated demand management (ADM) and setpoint control — using AI to adjust building systems dynamically based on real-time conditions, occupancy, or utility price signals.
For example, pre-cooling buildings in the morning to reduce afternoon peak loads can lower both emissions and demand charges — without impacting occupant experience.
These systems (like Noda) often leverage predictive models, reinforcement learning, or time-series forecasting to make adjustments autonomously, but also allow operators fine-grained control over zones and equipment to ensure that indoor comfort is maintained.
Best practice: Start small. Pilot ADM in one building or zone, monitor the impact, and refine from there. Ensure staff can override settings and build trust in the system before scaling.
Strategy #6: Embed ESG Into Day-to-Day Ops
The most successful ESG and sustainability strategies don’t live in a separate function — they are embedded into the daily rhythms of operations, maintenance, capital planning, and tenant engagement.
This requires new mindsets (and new data) as much as new tools:
- Facility teams need training on how operational decisions influence ESG goals.
- Sustainability leaders need access to real-time building data, not just annual reports.
- Asset managers overseeing capital planning and budgeting need to prioritize retrofit projects that reduce both emissions and energy cost.
- Vendors and contractors need to align scopes of work with measurable sustainability outcomes.
Best practice: Create cross-functional working groups (ESG, facilities, finance, IT) and have them meet regularly to review building/regional/portfolio performance, address shared tasks, and co-prioritize new initiatives.
Final Thoughts: From Reporting to Real Outcomes
Regulations like CSRD, SB253, and LL97 are raising the bar — and the cost of inaction. But compliance shouldn’t be the only motivation.
When done right, a well-implemented and managed ESG strategy can drive:
- Lower utility and maintenance costs
- Longer asset lifespans
- Higher tenant satisfaction
- Increased asset value through "green premiums"
- Reduced exposure to energy price volatility
The key is making ESG actionable. That means equipping the people who run buildings with the insights, tools, and support they need to move from data → insight → action → automation. Technology is part of the solution — but it’s strategy, process, and alignment that ultimately make it work.
Need a place to start? Focus on data visibility across your highest-energy buildings. Map your current ESG targets to operational levers. And identify a few high-impact, low-barrier optimizations to turn intent into impact – because a good ESG plan on paper is no longer enough — the next decade will belong to those who operationalize it.
About Noda
Noda is a data and analytics company on a mission to make every building smarter, more efficient, and more sustainable. Recently ranked in the top 10 tech companies leading the charge on climate action, its AI-powered suite of products surface unique insights that empower real estate teams to reduce costs, decrease time spent on routine work, and find and act on opportunities to save energy and carbon. Discover how Noda's solutions can unlock the potential of your assets and accelerate the transition to net zero. Visit us at noda.ai to learn more.