5 Hidden HVAC Faults That Are Quietly Driving Up Energy Costs in Hotels
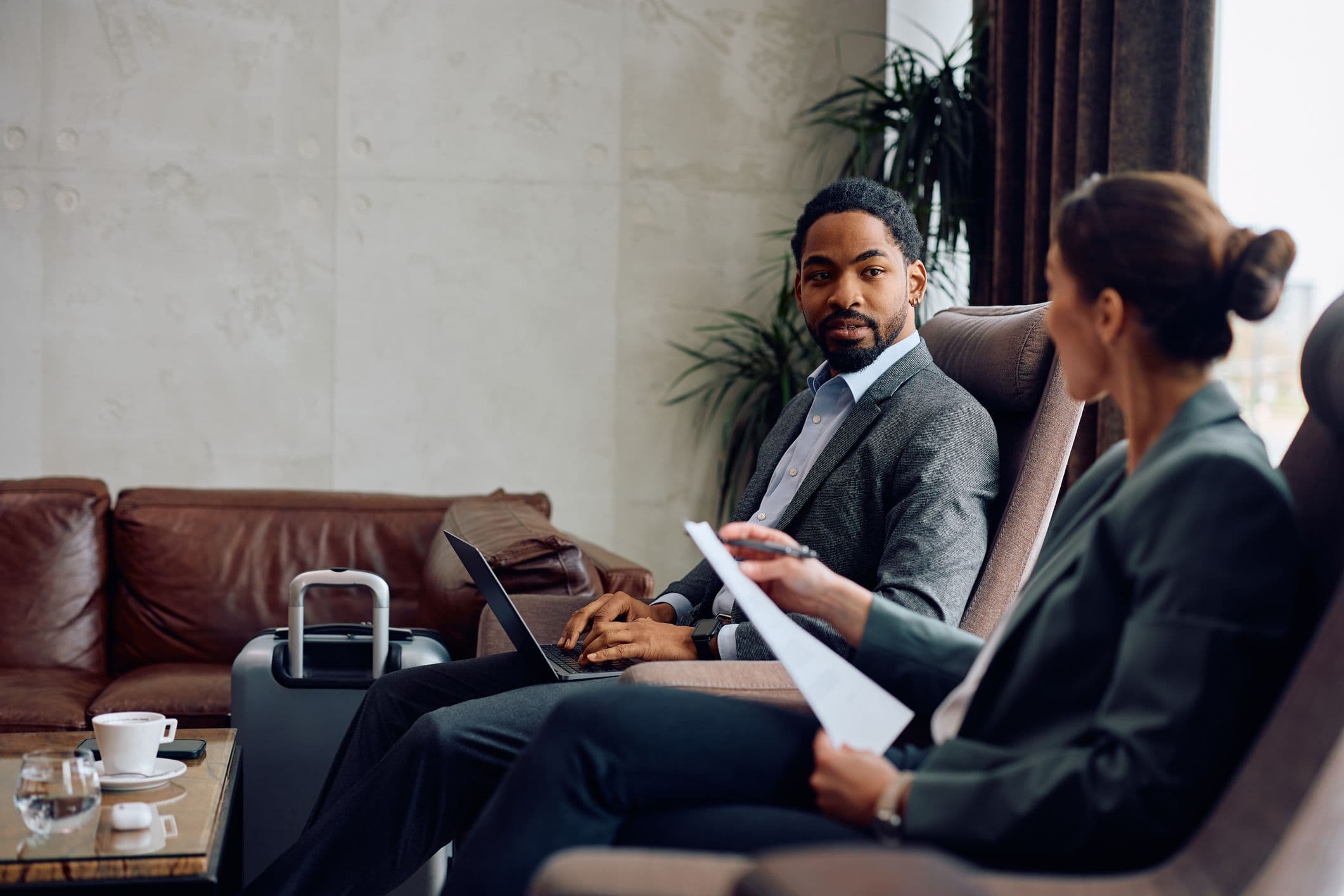
In the hospitality industry, comfort is currency. But behind the scenes of a perfectly climate-controlled lobby or a whisper-quiet guestroom HVAC system lies an often invisible culprit undermining both guest experience and operational efficiency: unnoticed equipment faults.
For hotel engineers, property managers, and asset owners, the challenge isn’t just technical — it’s economic. Many inefficiencies quietly drain energy budgets every month, compounded by inconsistent maintenance practices, evolving occupancy patterns, and decentralized facility oversight. And most of the time, they go unnoticed.
But with the rise of fault detection and diagnostics (FDD) technologies — fueled by smarter building data and AI — that’s changing. Let’s explore how fault detection can illuminate the unseen, chronic energy losses in hotels, and what operators can do about it.
Why Energy Waste in Hotels Often Goes Unnoticed
Hotels are among the most energy-intensive commercial property types, with HVAC systems alone often accounting for 40% of energy usage. Yet many properties still rely on reactive maintenance or time-based checklists, rather than real-time performance data.
Consider these common — yet hidden — examples of HVAC inefficiencies in hospitality:
- Overcooling in Unoccupied Spaces: A conference room set to 68°F overnight with no bookings.
- Mode Mismatch: A rooftop unit simultaneously calling for heating and cooling.
- Faulty Setpoints: A guestroom’s fan coil unit running constantly, even with no occupants.
- Short Cycling: A system toggling between heating and cooling due to poor sensor placement.
- Fan Left in "Hand" Mode: Equipment bypassing automation entirely, running 24/7.
Each fault may appear minor in isolation, but across a 200-key hotel, the energy waste can balloon quickly. More critically, these faults aren’t always visible on the BMS interface or to on-site staff. That’s where modern fault detection systems step in.
What Is Fault Detection and Diagnostics (FDD) for Hotels?
Fault Detection and Diagnostics systems continuously analyze building performance data to flag abnormal behaviors or deviations from expected performance. Rather than waiting for comfort complaints or asset failures, FDD surfaces issues proactively — often weeks or months before manual inspections would catch them.
Modern FDD platforms apply a range of techniques:
- Rule-based logic: Flags known patterns like “AHU cooling while space temp is below setpoint.”
- Machine learning models: Detect patterns and anomalies in time-series data.
- Contextual layering: Combines weather data, schedules, occupancy, and setpoints to refine fault accuracy.
In hospitality, FDD serves as a digital assistant to engineering teams, helping prioritize issues that impact comfort, energy costs, and guest experience.
5 Common HVAC Faults Costing Hotels Thousands Every Year
Hospitality environments are dynamic: rooms change hands daily, HVAC loads vary hour to hour, and comfort expectations are high. Faults often emerge not from major equipment failures, but from day-to-day operational drift.
Let’s break down a few fault types frequently flagged in hotels:
1. Fan Running in Unoccupied Mode
- What it is: A supply fan continues running during scheduled unoccupied periods.
- Why it matters: Drives unnecessary energy use — especially during shoulder seasons when ambient temps may not justify HVAC loads.
- Real-world context: In medium to large hotels, a single AHU running during unoccupied hours can consume over 1,500 kWh per month — translating to $200 or more in excess energy costs, depending on local utility rates. Multiply that across multiple units and sites, and these “invisible” faults can quietly add thousands to monthly energy spend.
2. Unnecessary Heating and Cooling
- What it is: Equipment operates when space temps don’t call for it (e.g., cooling on while setpoint is already met).
- Why it matters: Wastes energy and adds wear to equipment.
- Hidden culprit: Sensor drift, improper deadbands, or default setpoints during low occupancy seasons.
- Real-world context: Even small temperature mismatches can drive significant waste. For example, heating a space that's already above its heating setpoint — or cooling one already below its cooling threshold — can add 3–7% to monthly HVAC energy use. In properties with dozens or hundreds of zones, these control logic misfires can quietly compound into tens of thousands of dollars per year in avoidable spend.
3. HVAC Equipment Operating in the Wrong Mode
- What it is: A system is in heating mode when it should be cooling (or vice versa).
- Why it matters: Reduces comfort and increases energy use — while masking as a comfort issue rather than an energy problem.
- Real-world context: Mode mismatches — where equipment is calling for heating when it should be cooling (or vice versa) — often stem from faulty logic or sensor drift. These faults don’t just waste energy; they directly impact guest comfort. In one hospitality portfolio, a single zone VAV operating in the wrong mode for a week added an estimated 200–300 kWh of excess energy use, not to mention guest dissatisfaction from rooms being “too hot” despite active cooling.
4. Short Cycling Between Heating and Cooling
- What it is: An air handling unit rapidly alternates between heating and cooling.
- Root causes: Poorly placed sensors, oversized equipment, or narrow setpoint deadbands.
- Impact: Shortens equipment life, elevates energy bills, and destabilizes zone comfort.
- Real-world context: Short-cycling between heating and cooling modes — often due to tight deadbands or poor sensor placement — causes efficiency losses of 5–15%, and can severely reduce equipment lifespan. For a typical 15-ton rooftop unit, even moderate cycling can lead to hundreds of dollars in wasted energy and maintenance costs per unit per year, especially in transitional seasons when day-night temperatures swing widely.
5. Systems Set to “Occupied” When the Site Is Closed
- What it is: Units run in full “occupied” mode outside of scheduled business hours.
- Common in: Hotel fitness centers, meeting rooms, or spas with misconfigured occupancy schedules.
- Real-world context: If AHUs remain in “occupied mode” during closed hours — such as overnight or during seasonal shutdowns — they often run at full ventilation and conditioning rates unnecessarily. Just one large AHU running eight extra hours daily could result in 8,000–10,000 kWh of unnecessary usage annually, or around $1,000–$1,500 in added cost — and that’s per unit.
These aren’t just theoretical. Each is a standard fault type identified by FDD systems (like Noda) used in hospitality environments today.
From Discovery to Dollars: Quantifying the Opportunity
Let’s make this real. Imagine a 300-room resort with a mixed-use facility: guest rooms, restaurants, conference spaces, and wellness amenities. Without fault detection, energy inefficiencies often go unnoticed until utility bills spike or guest complaints rise.
But with a fault detection layer analyzing real-time data, a hotel may discover:
- 5 AHUs with fans operating 24/7 due to override settings.
- 8 zones overcooled by 3°F during unoccupied hours.
- 3 VAV boxes leaking chilled air due to valve leakby.
Each of these faults can be resolved with low or no capital investment — just better awareness and faster fixes.
Making FDD Actionable: Prioritization, AI, and Operator Usability
Effective fault detection and diagnostics (FDD) isn’t just about identifying faults — it’s about delivering the right insights, to the right people, at the right time, in a way that supports action, not alarm fatigue.
In hospitality, where engineering teams are often lean and time-constrained, the goal isn’t to catch every possible fault — it’s to prioritize the most impactful ones. That’s where intelligent triage, powered by machine learning, becomes essential.
How fault detection tools avoid alert fatigue and support lean engineering teams
- Simple, actionable dashboards for facilities managers that highlight top-priority issues based on energy impact, comfort implications, and duration — not just a flood of red flags.
- AI-based prioritization that filters out low-impact noise and surfaces what actually needs attention, using context like occupancy schedules, weather, and historical fault persistence.
- Zone-level comfort overlays that help staff anticipate complaints before they happen — and resolve them before guests notice.
- Portfolio-wide benchmarking tools that help asset managers detect patterns (e.g., all hotels overcooling in March shoulder season) and standardize fixes across properties.
- Exportable reports for ESG and sustainability teams that connect site-level energy savings and fault resolution directly to corporate carbon and cost-reduction targets.
The best FDD tools don’t just create alerts — they eliminate guesswork. They translate thousands of data points into a manageable, prioritized to-do list that makes engineers, managers, and sustainability leaders more effective — without overwhelming them.
Beyond Energy: Secondary Benefits of Fault Detection in Hospitality
While energy savings may be the headline, the operational wins are often just as compelling:
- Improved guest satisfaction: Fewer hot/cold complaints, faster issue resolution.
- Longer equipment life: By catching issues early, wear and tear is reduced.
- Faster troubleshooting: Engineers spend less time diagnosing and more time resolving.
- More efficient staffing: Smaller FM teams can do more with less — critical as skilled trades become harder to recruit.
The Bottom Line: Smarter HVAC Management Without CapEx Upgrades
Hospitality operators today face a balancing act: improve sustainability, enhance guest experience, and reduce operating costs — all without major capital upgrades.
That’s where smart analytics, and particularly fault detection, offer a path forward. It’s not about replacing equipment, but getting more from what’s already installed. By turning energy data into action, hotels can uncover hidden costs, cut waste, and improve operations — all while keeping guests cool, comfortable, and coming back.
As the industry braces for a wave of carbon reporting regulations and investor scrutiny around operational efficiency, the “nice to have” nature of FDD is becoming a “need to have.”
If your property team still operates on reactive maintenance or BMS alarms alone, now’s the time to ask: What faults are we missing — and what are they costing us?
About Noda
Noda is a data and analytics company on a mission to make every building smarter, more efficient, and more sustainable. Recently ranked in the top 10 tech companies leading the charge on climate action, its AI-powered suite of products surface unique insights that empower real estate teams to reduce costs, decrease time spent on routine work, and find and act on opportunities to save energy and carbon. Discover how Noda's solutions can unlock the potential of your assets and accelerate the transition to net zero. Visit us at noda.ai to learn more.