How Can Industrial Tenants Optimize Energy Use
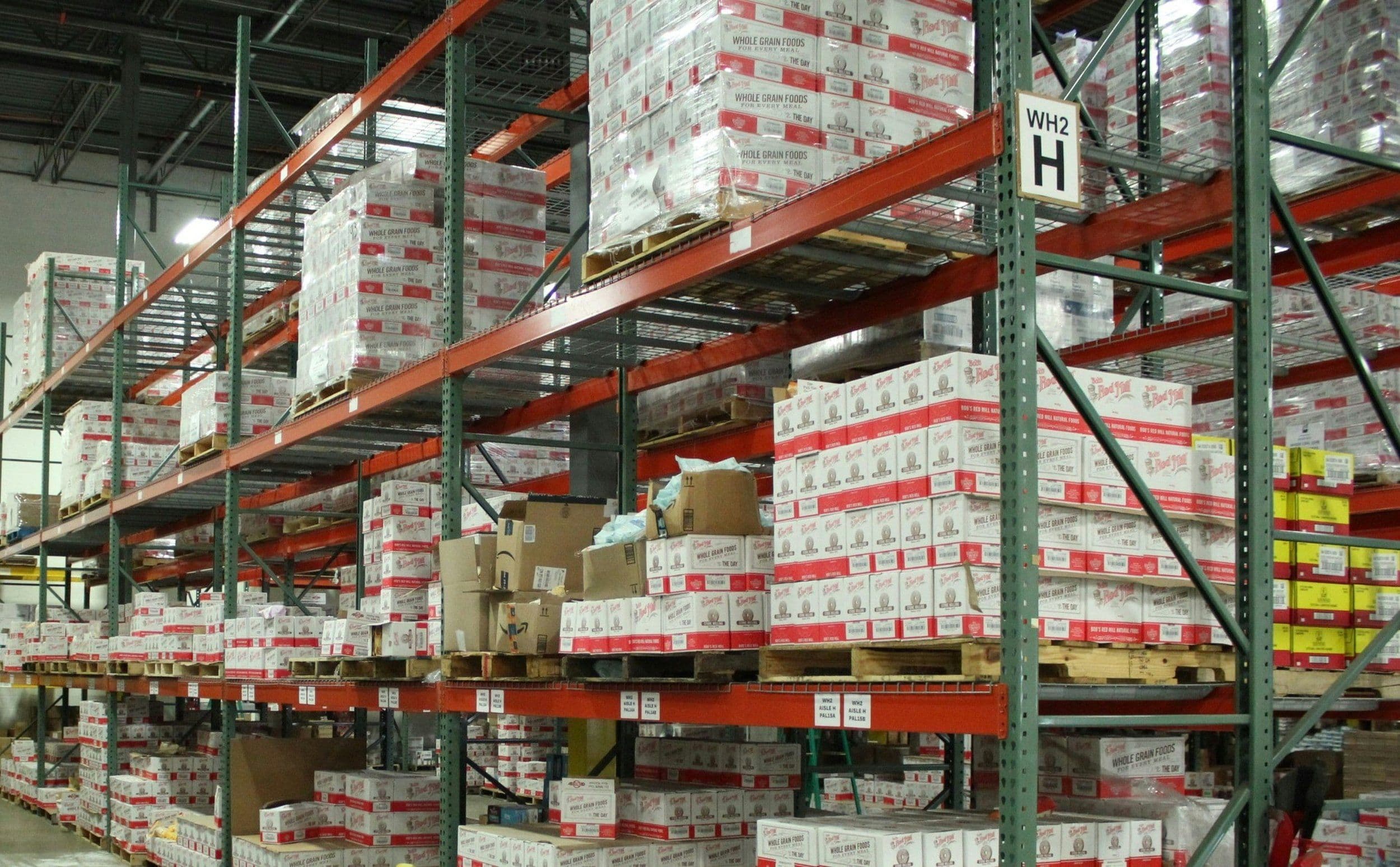
Companies in the industrial sector have a unique set of challenges when it comes to energy management in their commercial spaces. Whether you’re operating a manufacturing plant, distribution warehouse, or cold storage facility, managing and reporting energy consumption efficiently is critical when it comes to minimising downtime, optimising equipment performance, and boosting operational savings.
Thanks to recent advancements in data capture solutions and energy analytics tools, occupiers can take proactive control over their energy use, and create win-wins that support sustainability goals while cutting costs.
In this blog post, we’ll be taking a look at how corporate occupiers of industrial spaces can optimise the management of their energy use, cut costs, and improve sustainability performance.
What Types of Industrial Spaces Face Energy Management Challenges?
The industrial sector is made up of various categories of spaces, each has their own energy management challenges. Occupiers must understand the specific needs and energy use cases of their spaces and operations before they’re able to design and put effective energy strategies in place.
Let’s look at a few examples:
Distribution Centres & Warehouses
These often have very large footprints, 24/7 operational hours and high volumes of goods being stored, packed, and shipped. On average, warehousing costs can account for around 10% of a company’s total revenue. It's clear here there are opportunities to save energy. Typically high energy uses include HVAC systems, lighting, and equipment. Defining upfront where the key energy savings could lie, will shape the level of data you need to best identify high impact energy costs.
Cold Storage
Facilities storing perishable items, such as food, rely heavily on refrigeration systems. These systems consume significant amounts of energy (around 60% of all electricity used!), so ensuring optimal performance is crucial. Any system malfunction can result in spoiled goods and inventory loss, so organisations must ensure predictive maintenance practices are in place to reduce risks, loss of stock and prevent premature replacement of high cost machinery.
Light and Heavy Manufacturing
Manufacturing facilities can range from light assembly operations to heavy industries with complex machinery. In both cases, balancing energy efficiency while ensuring equipment remains in good working order is essential. Machines that are not optimised or properly maintained can lead to unexpected downtime, negatively impacting production, as well as wasted energy use that drives up costs and negatively impacts sustainability.
How Can Predictive Maintenance Help Minimise Downtime?
Minimising downtime is important for industrial tenants because every minute of lost productivity impacts revenue. One of the best ways to prevent unplanned downtime is through predictive maintenance - a highly cost effective method that can save roughly 8% to 12% over preventive maintenance, and up to 40% over reactive maintenance. Also known as ‘Industrial 4.0’, the use of predictive maintenance is expected to skyrocket between now and 2030:
Source: https://www.mdpi.com/2076-3417/12/16/8081
By using data from sensors and applying advanced technologies like AI, predictive maintenance allows companies to monitor the health of their machinery in real time, identify potential issues before they become critical, and schedule repairs only when needed. This proactive approach improves efficiency, minimises energy consumption, and boosts productivity, making it a very attractive option for businesses in the industrial sector.
Platforms like Infogrid’s integrate with Building Management Systems (BMS) and provide real-time data and alerts on equipment status. By analysing historical data and using machine learning to predict failures, occupiers can schedule maintenance during planned downtimes, ensuring uninterrupted operations and energy efficiency.
Additionally, fault detection and diagnostics further improve operational performance by identifying inefficiencies, such as overused or improperly maintained equipment. For example, if a refrigeration unit is consuming more energy than usual, predictive maintenance tools can flag the issue, allowing the tenant to investigate and resolve it before it leads to excessive energy use or equipment failure. Running a piece of equipment to the point of failure could cost up to 10 times as much as a regular predictive maintenance programme would, which really highlights the undeniable benefits of implementing this type of maintenance strategy.
How Can Industrial Occupiers Save on Energy Costs?
In many cases, industrial tenants will already have access to a wealth of energy data from sources like utility bills, interval data, and meters and submeters, thanks to typical industrial lease structures that grant tenants ownership of utility data via direct contractual relationships with utility providers. But the existence of data alone is not sufficient to drive a successful energy and sustainability program, especially when it is siloed across systems and not structured or formatted in a way that facilitates scalable management, reporting, and analysis. To maximise the use of available data, the right tools are essential for streamlining workflows and generating actionable insights.
Understanding Energy Consumption: Historical data from utility providers is a vital starting point for identifying energy usage patterns and potential inefficiencies. In the US, with most industrial occupiers paying their utility bills directly under triple-net leases, examining monthly bills is a natural first step in the journey. However, this process can quickly become unwieldy when multiplied across sites (and even multiple utility accounts within a single site). This is where technology can help. Cloud-based energy management platforms that integrate with utility providers can automate the centralisation and analysis of bill data, and installing integrated smart meters and advanced sensors can provide a more granular data layer, delivering real-time insights into energy consumption that drive optimisation of specific areas and equipment. For instance, real-time data analysis may reveal that lighting in a warehouse is active during non-operational hours, suggesting the need for improved controls or automated motion sensors.
Effective Tracking and Reporting: As noted above, simply having access to energy data isn’t enough; industrial tenants (like owners) must also analyse and report their usage (and the associated emissions) to truly meet the requirements of investors, shareholders, and regulators. Today’s energy management platforms (like those offered by Infogrid) apply a flexible reporting layer to real-time energy data, significantly streamlining the process of generating reports for internal and external stakeholders while also simplifying regulatory compliance and sustainability disclosures. Additionally, by using the insights that real-time energy data surfaces, occupiers can identify inefficiencies, make (and measure) progress towards corporate sustainability goals, and showcase material results to key stakeholders.
Making Progress on Sustainability Targets: Sustainability remains a key priority for companies across sectors, particularly as global regulations around energy efficiency tighten and companies across jurisdictions legally have an obligation to significantly reduce their carbon emissions by 2050. Manufacturing, logistics, and distribution companies are no exception. As the world continues to respond to climate demands from policymakers and consumers alike, firms are increasingly seeking to decarbonise their operations in line with corporate environmental goals (such as net zero) and regulatory requirements with fast-approaching deadlines between now and 2030. Effective energy management plays a key role in achieving these initiatives.
This is where advanced energy analytics solutions come into play. Infogrid’s platform supports sustainability projects by identifying energy-saving opportunities and helping organisations build sustainability plans. For example, by capturing detailed energy data across electricity, gas, and even water usage, occupiers can pinpoint inefficiencies and prioritise improvement projects. Infogrid’s machine learning capabilities also enable tenants to forecast the potential impact of these projects on energy consumption and carbon emissions, allowing for data-driven decision-making.
Beyond compliance, companies that embrace energy efficiency and sustainability can also benefit from enhanced brand reputation, as consumers and partners increasingly value eco-conscious business practices. In fact, attitude towards sustainability can make or break a company these days, with up to 80% of investors openly saying ESG factors are important in their investment decision.
Final Thoughts
Energy management is an increasingly critical part of the sustainability playbook, and a combination of data and technology is essential for firms in the manufacturing and logistics sectors to effectively advance their ESG goals. Thanks to advanced solutions (like Infogrid’s energy management and reporting platforms), occupiers can now harness the power of real-time data, predictive maintenance, and analytics to optimise energy consumption, minimise downtime, and reduce their carbon footprint.
Reach out to us today and find out how we can help you maximise your energy strategy.
About Noda
Noda is a data and analytics company on a mission to make every building smarter, more efficient, and more sustainable. Recently ranked in the top 10 tech companies leading the charge on climate action, its AI-powered suite of products surface unique insights that empower real estate teams to reduce costs, decrease time spent on routine work, and find and act on opportunities to save energy and carbon. Discover how Noda's solutions can unlock the potential of your assets and accelerate the transition to net zero. Visit us at noda.ai to learn more.